PHiLARC Products
- Carbon Steel Electrodes
- High Tensile Strength Steel
- For Low Temperature Steel
- Heat Resisting Steel Electrodes
- Atmospheric Corrosion Resisting
- Hardfacing Electrodes
- Stainless Steel Electrodes
- Nickel and Nickel Alloy Electrodes
- Cast Iron Electrodes
- Aluminum Alloy Electrodes
- Bronze and Copper Alloy Electrodes
- Gouging and Cutting Electrodes
- Solid Welding Wire (GMAW and GTAW)
- Oxy Fuel Gas Filler Rods for Brazing
- Oxy Fuel Gas Brazing FLuxes
- Submerged Arc Weding Wire and Flux
- Flux Cored Wires (FCAW)
PHILARC 308L
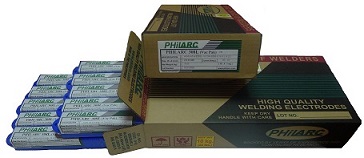
AWS Specification : AWS A5.4 E308L-16
JIS Specification: D 308L-16
Other Specif ication: DIN 8556 E19 9 L R 23
I. APPLICATIONS:
Fabrication of stainless steel structures and assemblies such as plate, pipework, vessels, tanks, forgings and castings in the chemical, petrochemical, power and pharmaceutical industries, food, drink and paper processing plant.
Highly recommended for general repair work and fabrication of stainless steel equipment such as containers, tanks, vats, and other equipment used in the dairy, chemical and food industries. Also ideal as protective overlay on steel where medium hardness and complete corrosion resistance is required.
Product |
Grade |
Plate
Forgings Castings
Pipe AISI stainless steels ASTM pipe ASTM castings |
BS 970 : Pt.1 : 1991 302S31, 304S11, 304S15, 304S31 BS 1449 : Pt.2 : 1983 304S11, 304S15, 304S16, 304S31 BS 1501 : Pt.3 :1990 304S11, 304S31 BS 1503 : 1989 304S11, 304S31, 304S51 BS 1504 : 1976 304C12, 304C15 BS 3100 : 1991 304C12, 304C15 BS 3605 : Pt.1 :1991 304S11, 304S31 201, 202, 301, 302, 304, 304L A312 Grades TP308, TP308L A351, Grades CF-3, CF-3A |
II. DESCRIPTION:
A general purpose stainless steel Shielded Metal Arc Welding electrode for welding 18/8 austenitic stainless steels. PHILARC 308L-16 deposits a low carbon 18% Cr-8% Ni weld metal to provide good corrosion resistance properties to intergranular attack from a range of liquid chemical media at service temperatures up to 300ºC. Welds with a smooth even metal transfer and stable arc, and is practically spatter free. Finely-ripped bead and self-peeling slag. Easy welding in all positions. The striking and restriking of the electrode is remarkably easy. A self releasing slag and the risk of porosity in the weld is minimal provided the electrode is dry. The finished welds exhibit a slightly concave shape with good cosmetic appearance which requires little or no post weld dressing. The electrode is ideal for both fillet and butt welding applications. The smaller sizes including 3.25mm are suitable for positional welding while the bigger sizes are for flat only.
III. NOTES ON USAGE:
Prepare and fit the work carefully, cleaning the joints of all foreign material. Use AC (minimum OCV of 70V) or DC+ current. Proceed with the lowest current possible and short arc without allowing coating to touch molten pool. Short and intermittent welding is to be preferred to avoid overheating and distortion. Avoid excessive weaving. Electrodes should be coated. Discard exposed core wire by striking or scratch welding in a scrap plate until exposed core wire is consumed. Use dry electrodes to prevent blowholes in deposit. If necessary re-dry at 200ºC for 2 hours before use.
IV. TYPICAL CHEMICAL COMPOSITION OF WELD METAL (%):
C |
Mn |
Si |
P |
S |
Cr |
Ni |
0.02 |
1.85 |
0.4 |
0.023 |
0.011 |
19.59 |
10.35 |
V. TYPICAL MECHANICAL PROPERTIES OF WELD METAL:
Tensile Strength N/mm2 (Ksi) |
Elongation % |
567 (82) |
47 |
VI. WELDING POSITIONS: ALL POSITION-EXCEPT VERTICAL DOWN
VII. SIZES AVAILABLE AND RECOMMENDED CURRENTS (AC or DC + ):
Size (mm) |
Dia. |
1.6 |
2.0 |
2.5 |
3.2 |
4.0 |
5.0 |
Length |
250 |
250 |
300 |
350 |
350 |
350 |
|
Current Range |
10-30 |
15-50 |
40-80 |
60-90 |
90-150 |
110-180 |
|
|
10-30 |
15-50 |
40-80 |
60-90 |
90-150 |
100-170 |
APPROVAL: ABS